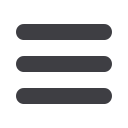
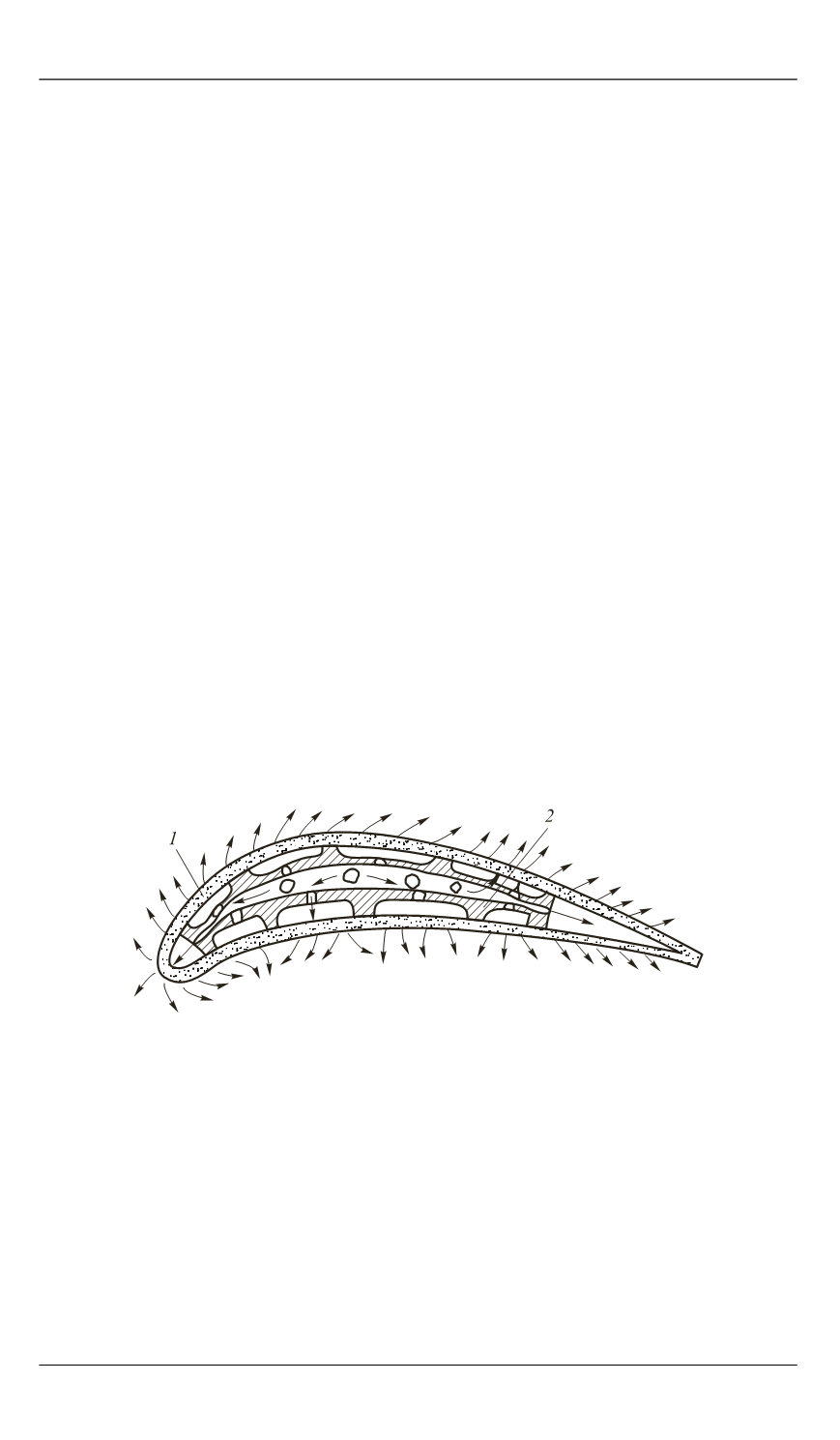
Особенности технологии изготовления турбинных лопаток с пористым охлаждением
5
проведен комплекс исследований, на основе которых получена ТЛ с
оболочкой из ПСМ (рис. 1). При изготовлении пористых элементов
для оболочек использованы тканые сетки с квадратными ячейками
№ 014 (ТУ 14-4-501-14) из стали 12Х18Н10Т, которые подвергали
травлению в растворе из HNO
3
, H
2
SO
4
,
KF
.
Затем сетки собирали в
брикет под углом 45º одна относительно другой и помещали в сталь-
ные контейнеры (конверты), в которых создавался вакуум 5·10
–1
мм
рт. ст. Время нагрева контейнера при температуре 1180…1200 ºС со-
ставляло 7…10 мин. Относительное обжатие брикета в процессе горя-
чей прокатки должно обеспечивать образование сварных соединений
проволок сеток и требуемые свойства ПСМ. После прокатки при ком-
натной температуре листовая заготовка извлекалась из контейнера.
Толщина изготовленного таким образом ПСМ составляла 0,7 мм,
пористость П = 0,43, размер пор 100 мкм, предел прочности σ
в
=
= 105 МПа, а относительное удлинение при разрыве δ = 11 %.
Технологический процесс гибки опытной партии оболочек ТЛ из
ПСМ заключается в последовательном деформировании листовой
заготовки в штампе с эластичной подушкой [5].
При листовой штамповке оболочек ТЛ изделия с радиусом гибки
передней кромки оболочки, равным 2 мм, получены без трещин и
расслоения ПСМ. Однако в результате пружинения заготовки не до-
стигается полного прилегания оболочки к корпусу лопатки (см. рис. 1),
что затрудняет процесс соединения ее с ребрами.
Рис. 1.
Конструкция турбинной лопатки с пористым охлаждением:
1
— пористая оболочка;
2
— корпус (силовой стержень) лопатки
Консолидацию оболочки с корпусом выполняли диффузионной
сваркой на установке типа СДВУ в приспособлении, представляю-
щем собой калибровочный штамп, в котором оболочка прижимается
к ребрам по всему контуру ТЛ. Температура диффузионной сварки
1200…1220 ºС, глубина вакуума 1·10
–3
мм рт. ст., время сварки
20 мин. Сила, прикладываемая к свариваемым заготовкам в штампе,
составляла 20 кН, нагрев осуществлялся индукционным устройством.